Corrosion Protective Zinc Coating Systems
Written by: Baril Coatings USA
Posted: April 24, 2023
updated on June 12, 2023
Corrosion presents manufacturing industries with extraordinary challenges when dealing with metallic alloys. From oil and gas processing to transportation infrastructure and beyond, corrosion can significantly impact metal structure longevity, performance, cosmetics and even safety. An extremely effective way of combating corrosion is to use a Zinc Rich Coating System which we'll discuss in depth in this latest article on Industrial Coatings.
Image of corrosion protective zinc coating on Industrial Pipes
Understanding Corrosion and Its Underlying Causes
Corrosion results from the deterioration of material when it reacts with its surrounding environment. While corrosion can happen with any type of material, it's most common with metallic alloys. Typically, corrosion is caused by reactions between moisture, hydrogen, electrical currrents, bacteria and even stress can induce corrosion when steel cracks under pressure.
One type of corrosion most are familiar with is rust, a specific type of corrosion that occurs from moisture and air oxidizing with one another. Often the first signs of rust appear as small specs on the surface yet they are actually tiny pits which grow from condinued oxidation.
Importance of Zinc Coatings
Zinc coatings are crucial these reasons and more:
- Protection against corrosion and undercutting resulting from damage when using standard coating systems.
- Prevention of rust through extended exposure or inadequate corrosion resistance.
- Avoidance of crevice corrosion due to poor coverage or the use of standard coating systems.
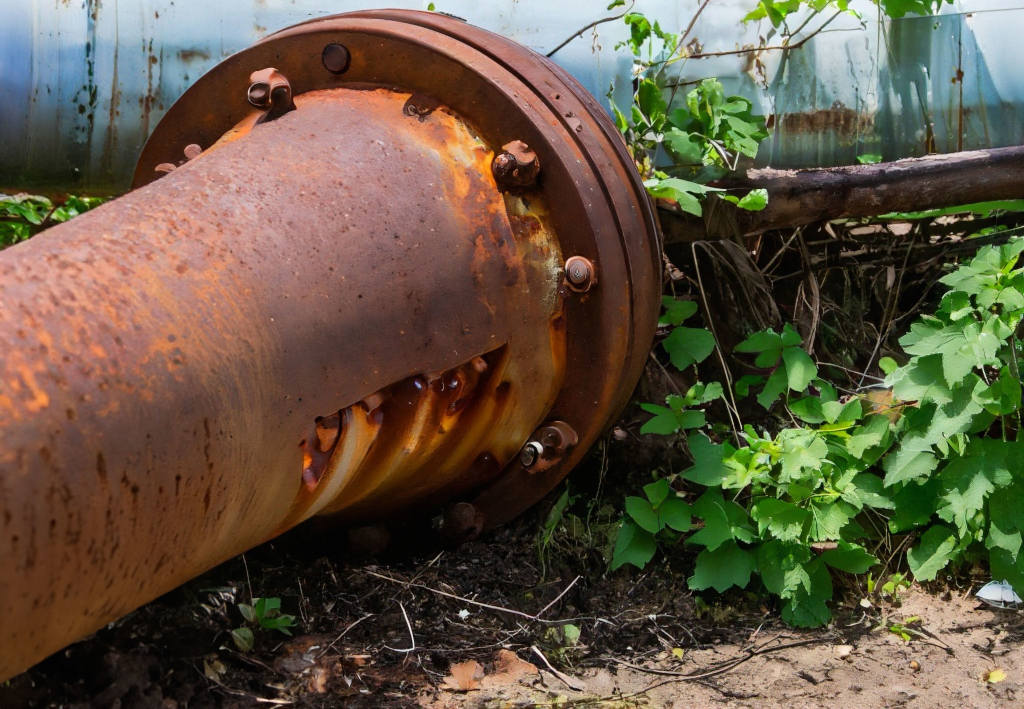
Zinc Coating Technology and Benefits
Zinc coatings provide two levels of corrosion protection when applied directly to a steel surface. Being an electro-positive element, zinc forms a cathodic protective barrier with a low corrosion rate of less than .01 mil per year, offering extended service life. Furthermore, zinc is sacrificial and protects steel from atmospheric conditions that produce corrosion.
Zinc Primer Benefits
Zinc-coated bolts demonstrate the sacrificial properties and superior protection offered by zinc coatings. See below for an example of how zinc coated bolts remain clean of all forms of corrosion even after a decade plus of use in incliment weather:
Maximizing the Benefits of Zinc Primer
To get the most out of zinc primer, we recommend following these steps:
- Surface Preparation: Blast the metal surface to a profile of .75 to 2.5 mils (SSPC-SP-5 White Metal Blast or minimum SSPC-SP-6 Commercial Blast) to create a suitable foundation for zinc adhesion and protection.
- Promote Adhesion: Ensure that the zinc coating is in direct contact with the metal surface for optimal adhesion and sacrificial qualities.
- Application: Apply the zinc coating using low-pressure conventional air spray or high-pressure airless spray, maintaining a minimum thickness of 3 mils above the blast profile.
- Corrosion Protection: Most primers contain zinc pigments necessary to protect against corrosion from road chemicals like magnesium chloride, calcium chloride, and natural corrosives like salt and moisture.
Bad Surface Prep Equals Bad Results
The below photo is an example of what not to do! Always properly prepare the metal alloy surface prior to putting on any type of protective coatings.
Zinc Coating Application Technologies
There are several methods used to apply zinc coatings, each with their own pros and cons as we'll cover below:
- Electroplating - Dip
- Galvanizing - Dip
- Inorganic Zinc - Spray
- Organic Zinc Rich - Spray
Electroplating - Dip
Electroplating is a metal finishing process in which a thin layer of metal, such as zinc, is deposited onto the surface of a substrate, typically a metal object, to provide a protective coating or decorative finish. The process involves immersing the object to be coated in a solution called an electrolyte, which contains ions of the metal to be plated. The object acts as the cathode (negative electrode), while a piece of the plating metal serves as the anode (positive electrode).
During the electroplating process, an electric current is applied to the electrolyte solution, which causes the metal ions to be reduced and adhere to the surface of the object being plated. The thickness of the deposited metal layer can be controlled by adjusting the duration and intensity of the electric current.
Electroplating with zinc, also known as zinc plating or zinc electroplating, is commonly used for corrosion protection of steel and iron components. The zinc layer forms a barrier between the substrate and the environment, preventing direct contact with corrosive elements such as moisture, oxygen, and salts. In addition, zinc acts as a sacrificial anode, meaning that it will corrode preferentially to the underlying substrate, thereby further protecting the base metal from corrosion.
Advantages of Electroplating - Dip:
- Uniform coating: Electroplating can provide a uniform and consistent coating thickness over complex geometries, making it suitable for various applications.
- Enhanced appearance: The process can improve the appearance and aesthetic value of the object by providing a shiny, smooth finish.
- Corrosion protection: Zinc electroplating offers excellent corrosion resistance, particularly for steel and iron substrates.
- Cost-effective: Electroplating can be a cost-effective method for applying thin protective layers to large volumes of small to medium-sized parts.
Disadvantages of Electroplating - Dip:
- Limited to conductive materials: Electroplating can only be performed on electrically conductive substrates.
- Thickness limitations: The process is most suitable for depositing thin layers of metal; achieving thick coatings may require longer processing times and increased costs.
- Environmental concerns: The electroplating process involves the use of chemicals and generates waste that must be managed according to strict environmental regulations.
- Incomplete coverage: In some cases, electroplating might not be able to reach every area of a complex part, leaving some surfaces uncoated and susceptible to corrosion.
Overall, electroplating is a widely-used method for applying zinc coatings to metal substrates, providing corrosion protection and enhancing the appearance of the finished product. However, the process may not be suitable for all applications, and alternative methods such as galvanizing or zinc-rich paint may be more appropriate depending on the specific requirements.
Galvanizing - Dip
Galvanizing, also known as hot-dip galvanizing, is a process where a steel or iron object is coated with a layer of zinc to protect it from corrosion. The method involves dipping the object into a molten zinc bath, typically at a temperature of around 840°F (450°C). The zinc forms a metallurgical bond with the steel, creating a durable and robust protective coating.
During the galvanizing process, the steel or iron object is first cleaned of any impurities, such as oil, grease, and mill scale, through a series of pre-treatment steps. These may include degreasing, pickling in an acid solution, and fluxing to promote the formation of a clean, reactive surface. The object is then immersed in the molten zinc bath, where the zinc reacts with the steel to form a series of zinc-iron alloy layers. Finally, the object is cooled, either by air or quenching in water, to solidify the zinc coating.
Advantages of Galvanizing - Dip:
- Long-lasting protection: The thick, adherent zinc layer formed during hot-dip galvanizing offers exceptional corrosion resistance, with a service life often exceeding 50 years in suitable environments.
- Complete coverage: The galvanizing process provides a uniform coating over the entire surface of the object, including edges, corners, and hard-to-reach areas, ensuring comprehensive corrosion protection.
- Low maintenance: Galvanized surfaces require minimal maintenance, as the zinc coating self-heals minor scratches and damage through the sacrificial action of zinc.
- Cost-effective: In the long term, hot-dip galvanizing is a cost-effective method for corrosion protection due to its durability, low maintenance requirements, and extended service life.
Disadvantages of Galvanizing - Dip:
- Size and shape limitations: The size and shape of the object to be galvanized are restricted by the dimensions of the zinc bath and the handling equipment.
- Aesthetics: The appearance of a hot-dip galvanized surface may not be as smooth and shiny as other coating methods, such as electroplating. Galvanized surfaces may exhibit a rough, matte finish with visible crystalline patterns known as "spangle."
- Incompatibility with certain materials: Some materials, such as aluminum, can be adversely affected by the high temperatures used in the galvanizing process, making them unsuitable for certain applications.
- Environmental concerns: The process generates waste materials such as zinc dross, ash, and pickling sludge that must be managed and disposed of in accordance with environmental regulations.
Hot-dip galvanizing is a widely used method for providing long-lasting, effective corrosion protection for steel and iron objects. The process ensures complete coverage and forms a strong bond between the zinc and the substrate. However, the method may not be suitable for all applications due to its limitations in size, shape, and compatibility with certain materials.
Inorganic Zinc - Spray
Inorganic zinc coatings, also known as inorganic zinc-rich primers or inorganic zinc silicate coatings, are a type of paint-like coating system that provides excellent corrosion protection to steel and iron substrates. The coating consists of zinc particles suspended in a silicate binder, which, when applied and cured, creates a highly adherent and durable protective layer on the metal surface.
The inorganic zinc coating is typically applied using spray equipment, such as airless or conventional air spray systems. The surface of the substrate must be thoroughly cleaned and prepared, usually by abrasive blasting, to ensure proper adhesion of the coating. The inorganic zinc coating can be applied as a single coat or as part of a multi-layer coating system, depending on the desired level of corrosion protection and the specific application requirements.
Advantages of Inorganic Zinc - Spray:
- Excellent corrosion protection: Inorganic zinc coatings provide a high level of corrosion resistance due to the galvanic action of the zinc particles, which sacrifice themselves to protect the underlying substrate from corrosion.
- High heat resistance: Inorganic zinc coatings can withstand high temperatures, making them suitable for use on structures and equipment exposed to elevated temperatures or in high-heat environments.
- Long-lasting performance: Inorganic zinc coatings are known for their long service life, often exceeding 20 years in suitable environments.
- Good adhesion: The inorganic silicate binder ensures strong adhesion to the substrate, as well as compatibility with a variety of topcoat materials.
- Abrasion and impact resistance: The cured inorganic zinc coating is highly resistant to abrasion and impact, providing added protection in harsh or demanding environments.
Disadvantages of Inorganic Zinc - Spray:
- Surface preparation: Inorganic zinc coatings require a high degree of surface preparation, such as abrasive blasting, to ensure proper adhesion and performance.
- Application conditions: The application of inorganic zinc coatings can be sensitive to temperature and humidity conditions, which can affect the curing process and the final coating properties.
- Recoat time: Inorganic zinc coatings may require a longer recoat time compared to other coating systems, which can potentially impact project schedules.
- Aesthetics: The appearance of inorganic zinc coatings can be somewhat rough or uneven, making it less suitable for applications where a smooth, glossy finish is desired.
Inorganic zinc spray coatings offer excellent corrosion protection and durability for steel and iron substrates, particularly in challenging environments or where high-temperature resistance is required. However, the application process can be more complex and demanding compared to other coating methods, requiring careful attention to surface preparation and application conditions.
Organic Zinc Rich - Spray
Organic zinc-rich coatings, also known as organic zinc-rich primers, are a type of corrosion-resistant coating system for steel and iron substrates. These coatings consist of zinc particles dispersed in an organic binder, such as epoxy, polyurethane, or acrylic. When applied and cured, the organic zinc-rich coating forms a protective barrier on the metal surface, providing galvanic protection through the sacrificial action of the zinc particles.
Organic zinc-rich coatings are typically applied using spray equipment, such as conventional air spray or airless spray systems. Proper surface preparation, like abrasive blasting, is essential to ensure good adhesion and performance of the coating. The organic zinc-rich coating can be used as a standalone system or as a primer in a multi-layer coating system, depending on the desired level of corrosion protection and specific application requirements.
Advantages of Organic Zinc Rich - Spray:
- Excellent corrosion protection: Organic zinc-rich coatings provide strong corrosion resistance due to the galvanic action of the zinc particles, which sacrifice themselves to protect the underlying substrate.
- Good adhesion and compatibility: The organic binder in the zinc-rich coating ensures excellent adhesion to the substrate and compatibility with a variety of topcoat materials.
- Ease of application: Organic zinc-rich coatings can be applied with standard spray equipment and are generally less sensitive to environmental conditions during application and curing compared to inorganic zinc coatings.
- Smooth finish: Organic zinc-rich coatings can provide a smoother, more uniform finish than inorganic zinc coatings, making them more suitable for applications where aesthetics are important.
Disadvantages of Organic Zinc Rich - Spray:
- Lower heat resistance: Organic zinc-rich coatings generally have lower heat resistance compared to inorganic zinc coatings, which may limit their use in high-temperature applications.
- Surface preparation: Thorough surface preparation, such as abrasive blasting, is required to ensure proper adhesion and performance of the organic zinc-rich coating.
- Potentially shorter service life: Organic zinc-rich coatings may have a shorter service life compared to inorganic zinc coatings, depending on the specific binder and environmental conditions.
Organic zinc-rich spray coatings offer excellent corrosion protection and a smoother finish for steel and iron substrates, making them suitable for a wide range of applications. However, they may have limitations in high-temperature environments and may require careful surface preparation to ensure optimal performance.
The best system depends on factors like equipment cost, part size, EPA restrictions, ease of application, and required service life.
Zinc Performance Testing and Baril Coatings History
Baril Coatings' zinc products have undergone rigorous testing, meeting high-performance standards. The company has a 50+ year history of providing high-performance zinc products for C1-C5 marine environments, with applications ranging from DOT light poles to oil and gas equipment.
Zinc Primers by Baril Coatings
- SteelKote 826 Epoxy Zinc Primer (50% Zinc Load)
- SteelKote 829 Zinc Primer (Over 80% Zinc Load)
- DualCure 306 ZRU Moisture Cure Zinc Rich Urethane Primer (Over 80% Zinc Load)
SteelKote® 826 Epoxy Zinc Primer
SteelKote® 826 Epoxy Zinc Primer: This high-solids, two-component epoxy zinc primer is designed for OEM manufacturing and commercial vehicles. It offers easy application, good flow, excellent corrosion protection, and long-term durability. When applied, the ready-to-spray VOC is 2.8 lbs. per gallon.
SteelKote® 829 Zinc Rich Epoxy
SteelKote® 829 Zinc-Rich Epoxy: This high-solid, two-component, 84% zinc-rich epoxy primer is designed for OEM manufacturers and commercial vehicles. It offers easy application, good flow, and superior corrosion protection against undercutting, and creepage, and has passed 5,000 salt spray resistance. Its mixed VOC is 2.5 lbs. per gallon, and it meets the ASTM D520 classification.
DualCure® 306 Zinc Rich Urethane
DualCure® 306 Zinc-Rich Urethane: This high-solid, 86% zinc-rich urethane primer is designed for OEM manufacturers and commercial vehicles. It offers easy application, high build, and superior corrosion protection. This product has passed 10,000 salt spray hours, 9A gravelometer, and 5,000 hours of magnesium chloride testing. It also meets the ASTM D520 classification.